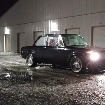
I discovered that the shaft collar for the throw-out / release bearing was contacting the splined part of the spring pack on the clutch friction disc.
I contacted gripforce clutches and they confirmed that the friction disc needs to be installed with the spring pack facing the flywheel into the recessed portion of the flywheel, which is not typical. The clutch kit only comes with generic instructions showing the spring pack of the friction disc facing away from the flywheel. After making sure that the release bearing slid freely on the collar, everything clutch related went back on the engine and torqued to spec.
Getting the engine back in. My first approach was to install it form the bottom, but that was huge pain. So, I rigged the engine differently to the hoist and installed the engine from the top, and then installed the transmission from the bottom. The 10 foot steel cable was used as a safety just in case the bolt holding the engine to the chain gave way. Then, I reinstalled the driveshaft and then the exhaust... again!
I ordered an O2 plug which will be installed when it arrives this week.
Installing the engine this way is so much easier. Right now, I am using a cheapy parts store ignition switch to start the car, which I will swap out once I get the new part. Now, I have to clean up the wiring... again. But hey it runs! There is link below to a pretty crude video of the engine running. Dust blowing everywhere as I rev the engine. I am leaving the flares, front spoiler, and hood off or now. They will be the last things to go on the car, which should be very soon.
BMW 2002 S54 Swap 480p.mov
- Read more...
- 6 comments
- 12,605 views